With the cross-domain development of ICT technology in the past two decades, IP network has gradually become the key infrastructure for people's life and work as well as social and economic development. The bandwidth of the IP network has increased hundreds of times. The router, an network element (NE) in the IP network, is facing huge challenges in power supply and heat dissipation deployment, energy saving and emission reduction as its platform capability has evolved from 2.5G/slot to 1T+/slot and its power consumption has increased from 2 kW to 20 kW.
In this paper, the energy efficiency of large-capacity NEs is analyzed and discussed from the aspects of power consumption structure, energy-saving methods and technologies, and the benefits and deployment.
Power Consumption Structure
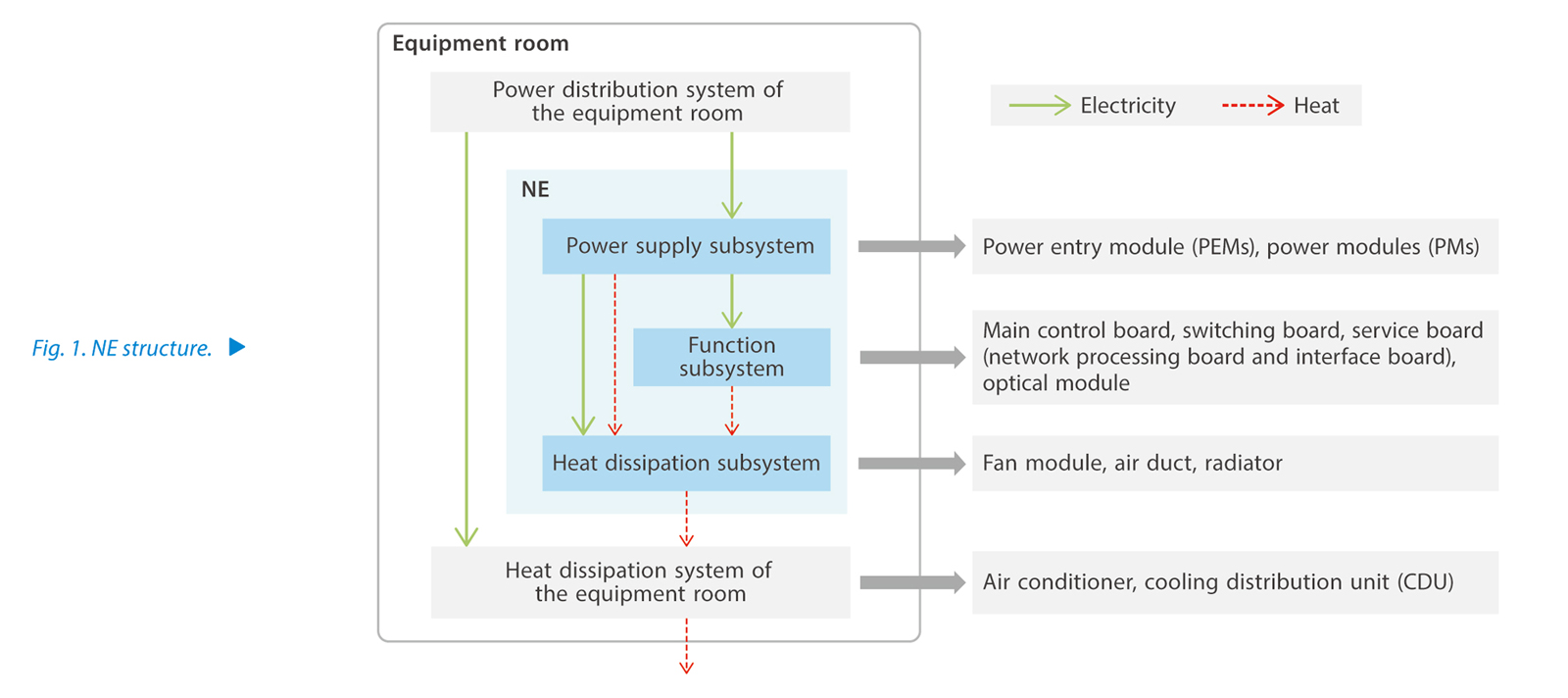
From the perspective of power consumption, the structure of a router consists of three subsystems: function subsystem, heat dissipation subsystem, and power subsystem (Fig. 1). The function subsystem is the main body of the router, responsible for service processing like receiving/transmitting of optical signals, and data packet forwarding. It consumes a lot of electricity, while generating a large amount of heat. The heat dissipation subsystem is an important part of the router, responsible for dissipating the heat generated inside the device to ensure that the components of the function subsystem operate properly, which consumes a large amount of electricity during this process. The power subsystem is connected with external power distribution systems, converts the input power supplies, and provides power for both the function subsystem and the heat dissipation subsystem. It consumes some electricity. In addition to the heat dissipation subsystem of the router, the heat dissipation system of the equipment room also needs to consume a large amount of electricity to dissipate the heat generated by the router into the outdoor air.
The actual power consumption of the router may vary with the implementation solution, operating environment, service deployment, and traffic load, and its power consumption structure may also be different. Fig. 2 shows the power consumption structure of ZTE's large-capacity equipment with full hardware configuration and full load at normal and high temperature respectively. The power consumption of service boards in the function subsystem accounts for about 60–70%, and is 15% higher at high temperature than at normal temperature. The power consumption of the heat dissipation system accounts for about 15–25%, and is 125% higher at high temperature than at normal temperature.
For the equipment with the same thermal density and heat, the energy efficiency ratio (EER) of the heat dissipation system in the equipment room varies greatly with the air distribution and heat dissipation technologies. To dissipate the heat of 10 kW, the power consumption of the air-conditioning system in a traditional equipment room is at least 5 kW, while the power consumption of liquid-cooled CDU is not more than 500W.
Energy Saving Methods and Technologies
The energy saving methods and technologies are discussed from the function subsystem, heat dissipation subsystem, and power supply subsystem of the equipment according to the analysis on its power consumption structure.
Function Subsystem
The function subsystem is the main body of equipment power consumption. The actual consumption is determined by hardware design solution, component operating status, and component traffic load. Therefore, the power consumption of the function subsystem can be reduced from the following aspects:
—Hardware design solution: With the continuous increase of IP network bandwidth, the capacity of the equipment platform has doubled almost every 2–3 years in the past decade. The chips with higher integration, more advanced manufacturing process and larger capacity are used to reduce the number of chips on a single board and lower the chip-level power consumption per unit capacity and the power consumption of inter-chip communication. This can effectively slow down the growth trend of overall power consumption and reduce EER.
—Component operating status: When the equipment is deployed, many board components are installed. Generally there are some components that are not officially enabled but are powered on and consume energy. Therefore, if the power-on/power-off function of service board components is supported and controled as required, the actual power consumption of the function subsystem can be effectively reduced. To ensure high system reliability, key components like main control boards and switching boards are generally not powered off.
—Component traffic load: The actual power consumption of board components is affected by traffic load. The more complex the services, the higher the traffic load, and the higher the chip power consumption. The core chips have been able to automatically adjust power consumption in real time according to load changes. On this basis, energy saving can be considered from two levels. At the chip level, a large-capacity forwarding plane chip usually consists of different function units. Theoretically, some function units of the chip can be turned off based on the actual service type, traffic load, and interface enabled to save more energy. This method requires the support of chip-level features and intelligent software analysis and control features. In actual deployment, there is uncertainty about the impact of the function units that the chip turns off on actual services as well as the time and mode of restarting the function units. At the network level, generally there are a large number of parallel links for IP network node interconnection. When the traffic load is low, some of these links can be shut down to save energy. If the disabled links correspond to one interface board or service board, the corresponding board can be powered off to maximize energy saving. When the traffic load increases, the disabled links or the powered-off board needs to be restored. If the parallel links are members of the LAG interface, the NE itself can perform intelligent analysis and restoration. If the parallel links are members of route load sharing, the centralized controller is required to implement network-level analysis and management.
Heat Dissipation Subsystem
The power consumption of the heat dissipation subsystem mainly comes from the rotation of fans. The fans consume more electricity as its rotational speed increases. The fan speed is also related to chip temperature, system air duct, radiator, and fan efficiency. Therefore, the power consumption of the heat dissipation subsystem can be reduced from the following aspects:
—Advanced air duct design: At the system level, independent air ducts are designed in different areas, and front-to-back I-type or Z-type air ducts are employed to shorten the air duct path. At the component level, the chip layout is optimized to reduce wind resistance of the path.
—Advanced radiators and fans: Advanced heat conduction technologies such as phase change radiators and efficient thermal conduction interface materials are used to improve the efficiency of heat transfer from the chip to the air. Energy-efficient fans are used to consume less electricity and emit more heat.
—Intelligent fan speed control: Real-time precise closed-loop monitoring of chip temperature and fan speed is realized, and the chip temperature is controlled within the optimal operating temperature range with the lowest fan power consumption.
—Liquid cooling technology: The cold plate is used to dissipate heat for key chips with high heat density on the component, and the heat is transferred from the equipment to the CDU through the liquid-cooled media in the pipeline connecting the cold plate and the CDU. The CDU exchanges heat to the water cooling system of the air conditioner in the equipment room, and releases it into the outdoor air.
Power Subsystem
The power consumption of the power subsystem is reflected in the power conversion efficiency. The higher the power conversion efficiency, the lower the power consumption of the power subsystem. The power conversion efficiency is related to the number of power modules and power load. When the power load is low, the power conversion efficiency is relatively low.
Operators require full configuration of power modules for large-capacity NEs, while the number of power modules for large-capacity NEs is usually designed based on extreme conditions such as long-term evolution and high temperature conditions. As a result, the actual power load of the equipment may be relatively low, and the power conversion efficiency is not optimal. According to the actual power load of the equipment or the power load of the function subsystem in full configuration, appropriate redundant power modules can be added to turn off idle power modules. This helps to improve the power conversion efficiency, thereby reducing the power consumption of the power subsystem.
Benefits and Deployment
The benefits of energy efficiency vary greatly with different energy-saving technologies, and there are also differences in technology maturity and deployment risks, as shown in Table 1. It is recommended that operators deploy appropriate energy-efficient technologies based on their own conditions.
Conclusion ZTE has fully employed the self-developed chips with high integration, advanced manufacturing process and large switching and forwarding capacity in the function subsystem of its large-capacity IP NE, which can support component-level power-on/power-off. In the heat dissipation subsystem, it has used independent front-to-back I-type or Z-type air ducts in different areas, and has also adopted advanced thermal conduction technologies and energy-efficient fans to support intelligent fan speed adjustment and liquid cooling technology. The anhydrous liquid cooling system has been trialed on the operator's network, which can effectively reduce the noise and power efficiency usage (PUE) of the equipment room. Self-developed high-efficiency power modules have been used in the power subsystem, with a power conversion efficiency of up to 95%. ZTE has adopted advanced and mature energy-saving technologies in its large-capacity IP NEs, which will help operators reduce the power consumption of their equipment and auxiliary facilities and contribute to the green development of human beings.